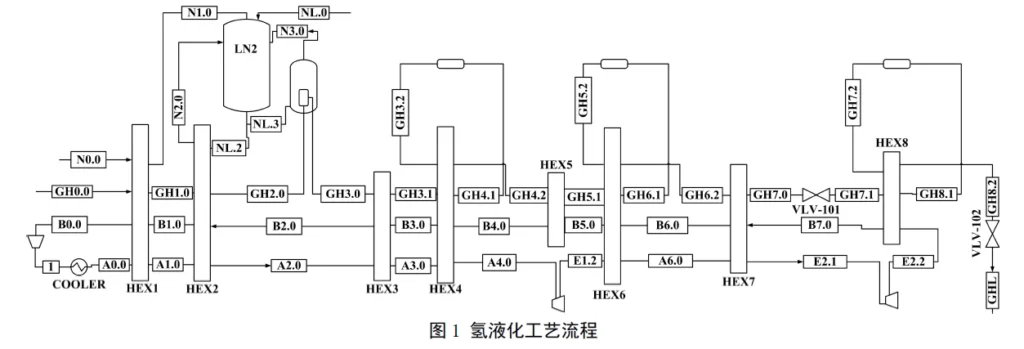
Process flow:
The raw material hydrogen enters the cold box, is pre-cooled by the primary heat exchanger HX-1 pre-cooled by cold nitrogen, and then enters the secondary heat exchanger HX-2 pre-cooled by liquid nitrogen for cooling, and then enters the primary positive heat exchanger soaked in liquid nitrogen. Parahydrogen converter for constant temperature conversion. The converted hydrogen is cooled by the third- and fourth-stage heat exchangers HX-3 and HX-4, and then enters the second-stage normal and parahydrogen converter for adiabatic conversion, and at the same time, it returns to the fourth-stage heat exchanger HX-4 for cooling after exothermic heating. . The cooled hydrogen is cooled by the fifth and sixth-stage heat exchangers HX-5 and HX-6, and then enters the third-stage normal-parahydrogen converter for adiabatic conversion, and at the same time, it returns to the sixth-stage heat exchanger HX-6 for cooling after exothermic heating. . The cooled hydrogen is cooled by the seven-stage heat exchanger HX-7, and then cooled by the J-T valve, and then cooled by the eighth-stage heat exchanger HX-8, and then enters the fourth-stage normal and parahydrogen converter for adiabatic conversion, while releasing heat. After warming up, it returns to the eight-stage heat exchanger HX-8 and enters the liquid hydrogen storage Dewar after cooling. The high-pressure helium discharged from the helium screw compressor is cooled by the water cooler, and then pre-cooled by the primary heat exchanger HEX1 pre-cooled by cold nitrogen, and then enters the secondary heat exchanger HX-2 pre-cooled by liquid nitrogen. Then enter the third and fourth-stage heat exchangers HX-3 and HX-4 to cool down to a lower temperature, and then pass through two-stage turbines in series. Eight-stage heat exchanger HX-8 low-pressure side inlet. The refluxed low-temperature and low-pressure helium gas flows countercurrently through the eighth to the first stage heat exchangers (HX-8~HX-1) to recover the cold capacity, and then leaves the cold box, and then returns to the suction end of the compressor for recirculation.
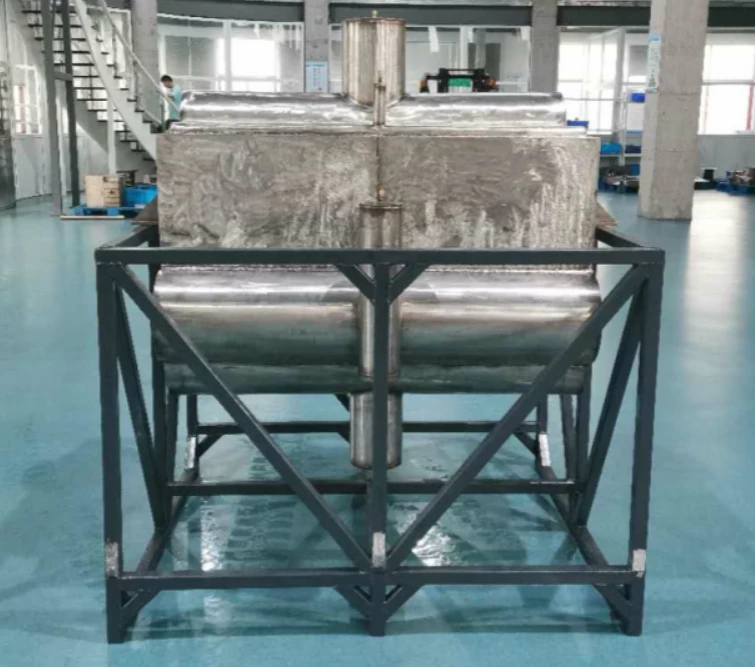
Fig. 2 Hydrogen liquefaction system and steel plate-fin heat exchanger for low temperature field
Comparative advantage:
Diffusion welding has no solder, high and low temperature resistance (-200℃~900℃), high compactness, high heat exchange efficiency, low leakage rate (1*10-9Pa·m3/s), and high welding strength (10MPa). At the same time, the secondary welding has no effect on the core weld and other advantages.
Comparative advantages: The heat exchangers used in the domestic hydrogen liquefaction system are mainly aluminum alloy plate-fin heat exchangers. Due to the strict requirements on the leakage rate of the products, the plates of the aluminum alloy plate-fin heat exchangers are selected to be thick, large in size, heavy in weight, And brazing problems such as leakage are not easy to repair. Aluminum alloy plate-fin heat exchangers and stainless steel pipelines will face difficulties such as welding of aluminum alloys and stainless steels.
The first domestic large-scale hydrogen liquefaction system developed and produced by Shenshi uses a diffusion welded stainless steel plate-fin heat exchanger to solve many of the above problems and fill the gap of steel plate-fin heat exchangers in the domestic hydrogen liquefaction field.