With the development of modern aerospace power systems towards high thrust ratio and high flight Mach number, the thermal load on the engine increases sharply. In order to guarantee the reliability and longevity of the engine, the development of rapid active cooling technology is crucial. The microchannel heat exchanger is considered to be an ideal choice to solve the problem of engine heat dissipation and cooling. It is composed of a core heat dissipation unit – a microchannel structure, and the heat is rapidly dissipated by forced convection through the cooling medium flowing through it. Microchannel heat exchangers have the characteristics of high heat transfer performance, compact structure, light weight, small size, easy integration and packaging, etc., and have significant advantages in aerospace engines.
At present, with the continuous progress of processing technology, micro-channel cooling technology has been applied in engine combustion chamber wall cooling, hypersonic aircraft precooler system, turbine blade heat dissipation and cooling, etc., in order to ensure the reliable operation of the engine and normal flight. played a vital role. The mainstream microchannel structure in the market is shown in the figure below.
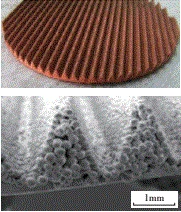
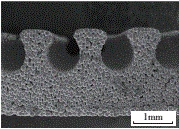
Application of Micro-channel Cooling Technology on Combustion Chamber Wall
In order to improve the cooling performance of the combustion chamber, reducing the cooling gas is the development direction of aero-engines. The use of micro-channel cooling technology can effectively reduce the temperature of the combustion chamber wall, and at the same time, the heat absorbed by the micro-channel can be used for fuel preheating, thereby realizing regenerative cooling.
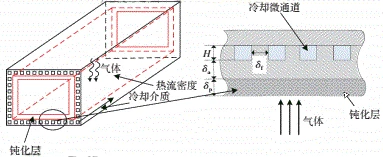
Application of Microchannel Cooling Technology in Precooling System
As a key component in the engine thermal cycle, the precooler can achieve high efficiency/rapid deep cooling of high-temperature air, thereby reducing the temperature to the normal working temperature of the aero-engine, and microchannel heat exchangers are often used to enhance its cooling performance.
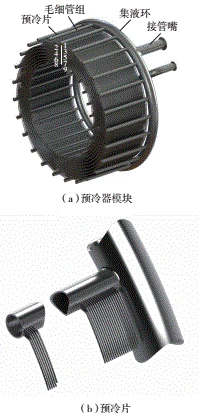
Application of Microchannel Cooling Technology in Turbine Blades
At present, the turbine inlet gas temperature of advanced aero-turbine engines reaches 1800~2050K, which is close to the temperature resistance limit of turbine blade materials. Cooling technology must be used to effectively cool the turbine blades. The cooling of turbine blades is mainly by machining microchannels inside the blades. The cooling methods such as air film and impact are adopted to achieve fast and efficient cooling through the airflow and blades in the microchannel. The following figure shows the cooling structure of a typical turbine blade.

At the same time as the rapid development of aerospace microchannel cooling technology, there are also many corresponding technical challenges that need to be further explored. There are relatively few domestic companies that have in-depth research, manufacturing and application of micro-channel cooling technology for aerospace engines, and Hangzhou Microcontrol Energy Saving Technology Co., Ltd. is one of the best. In 2017, the integrated precision microchannel heat exchanger project of Hangzhou Microcontrol subsidiary-Hangzhou Microcontrol was unanimously recognized by the judges, and won the third prize in the National Finals of the Second China Aviation Innovation and Entrepreneurship Competition.
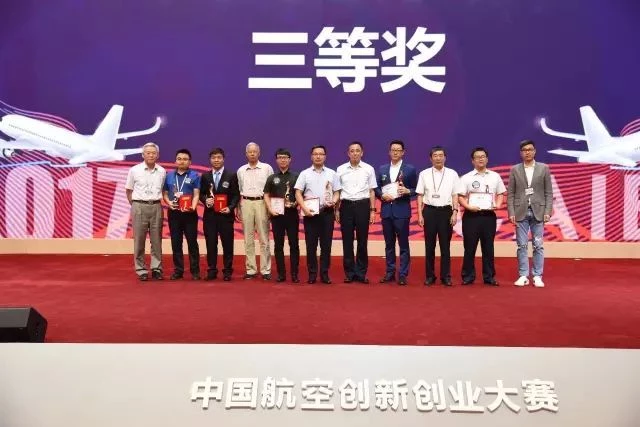
The high-efficiency and compact micro-channel heat exchanger for aerospace developed by Hangzhou Microcontrol is characterized by compact structure, high heat transfer performance, light weight and small size (reduced by 20%-30%). Its specific solutions include environmental control system. Use 10KW antifreeze-antifreeze heat exchanger (three-stream heat exchanger), 50KW fuel-hydraulic oil heat exchanger for aero engines, and air-refrigerant heat exchange micro-channel condenser for aerospace.