Hangzhou Microcontrol Energy Saving Technology Co., Ltd.
With the depletion of energy and the deterioration of the environment, the development and utilization of high-efficiency and clean new energy will become an important choice for energy development in the 21st century. Solid oxide fuel cell (SOFC) is a kind of direct conversion of chemical energy in fuel and oxidant. The all-solid-state electrochemical power generation device that generates electricity has high energy conversion efficiency, which can reach about 60%, and the heat generated by the cogeneration efficiency can reach more than 80%. It is currently the most cutting-edge and most technically difficult new fuel cell. The developed countries generally regard it as a strategic reserve technology. The FPHE series printed plate microchannel heat exchanger developed by Hangzhou Microcontrol Energy Saving Technology Co., Ltd. has been applied to SOFC and SOEC systems in many cases. In recent years, the company has continued to make efforts in this field to improve product quality and expand market share. Compare.
Solid oxide fuel cell is a device that uses electrochemical reaction to generate electricity. It has no Carnot cycle and its efficiency is much higher than other power generation equipment. It has a wide range of fuel applications and low manufacturing costs. The main products are CO2 and water. Located between 800 ℃ ~ 1000 ℃. The FPHE series of printed plate micro-channel heat exchangers developed by Hangzhou Shenshi have the characteristics of high temperature resistance above 1000 ℃, which is suitable for SOFC systems. FPHE adopts heat-resistant and anti-oxidative materials to ensure the effective heat exchange of SOFC’s high temperature exhaust gas at 850 ℃. On the other hand, the diffusion welded plate-fin heat exchanger adopts a high-efficiency heat exchange fin structure to effectively improve the heat exchange efficiency, and the volume of the heat exchanger can be greatly reduced. The three-in-one multi-flow heat exchanger developed by Shen’s innovatively integrates multiple heat exchangers in the SOFC power generation system into one heat exchanger. While the SOFC power generation system operates effectively, the number of parts is reduced, and the SOFC power generation system can be realized. The need for system compactness.

The high-efficiency compact heat exchanger developed by Shenshi adopts the most advanced millimeter-level channel and diffusion connection technology in the world. It has high heat exchange efficiency, small size, light weight, high compactness, high structural strength, high pressure resistance (up to 99MPa). ), high/low temperature resistance (-200℃~1000℃), strong corrosion resistance, small thermal resistance, low leakage rate, wide range of applicable media, etc., and can adapt to complex working conditions. Product manufacturing adopts vacuum diffusion welding process, which does not need to add any solder, solid-state bonding between materials and materials, and the characteristics of diffusion welding joints are equivalent to the physical properties of the base metal. It effectively solves the operation problems of the heat exchanger under the conditions of high temperature, thermal shock, high life and low flow resistance.
It is the company mission of Hangzhou Shenshi to realize the green, efficient, safe and lightweight of the thermal management system with small and micro high-efficiency heat transfer structure technology. Continue to create value for users.
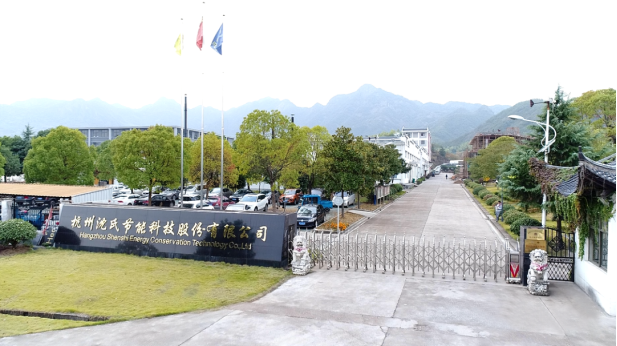
Hangzhou Microcontrol Energy Saving Technology Co., Ltd. is a wholly-owned subsidiary of Hangzhou Shenshi, focusing on the research and development, production, sales and service of printed plate microchannel heat exchangers. The company is located in Xinjiabo Science and Technology Park, Qiantang New District, Hangzhou. It has special equipment production qualifications, has domestic leading vacuum diffusion welding technology, and is committed to low-carbon thermal management solutions under the national “carbon peak, carbon neutral” strategy. The company is in the supply chain of LNG, hydrogen and other industrial gases and its green energy fields; in the fields of green power such as fuel cells, heat recovery power generation, and nuclear power; in the fields of thermal management of power systems such as aviation, ships, and vehicles; in aerospace, base stations, new In the field of environmental control such as energy vehicles and the field of micro-chemical industry, it provides energy-saving and material-saving low-carbon heat exchange solutions for users’ thermal systems.
The company is the first domestic manufacturer of high-efficiency and compact printed plate microchannel heat exchangers and microreactors, and the first (set) industrialized microchemical continuous reaction equipment general contractor in Zhejiang Province. The company has complete product qualifications, and has obtained ISO9001:2015, ISO14001:2015, GJB9001C-2017, UL/C, CE, ROHS, CRAA, A2 pressure vessel production license and DNV classification society certification.